|
|
|
содержание ..
1
2
3
4
5
6
7
8
9
10 ..
РУДНАЯ ЧАСТЬ ШИХТЫ ДОМЕННОЙ ПЕЧИ
В настоящее время основным железосодержащим сырьем для доменной плавки
является агломерат. Основное требование доменного процесса — всемерное
увеличение содержания железа в рудной части шихты — обеспечивается более
глубокой степенью обогащения руд. При этом руды измельчаются до
пылевидного состояния. Использование таких руд в агломерационном
процессе без предварительного окомкования приводит к ухудшению
газопроницаемости шихты и снижению производительности агломерационных
машин. Поэтому в мировой практике наметилась тенденция увеличения
производства окатышей.
Принципиальное отличие агломерата от окатышей состоит в том, что
агломерат — это продукт спекания мелкой руды, а окатыши — это продукт
обжига руды, предварительно тонко измельченной до 0,074 мм и
оком-кованной в шарообразную форму.
Сырьевая база большинства металлургических заводов представлена
железными рудами с кислой пустой породой (отношение Ca0/Si02 меньше
1,0). В доменной плавке для получения чугуна с минимальным содержанием
серы основность шлака (отношение Ca0/Si02) поддерживается значительно
выше 1,0. Дополнительное количество сырого известняка обычно вводят в
шихту при производстве агломерата и окатышей. Часто оказывается
целесообразным для кратковременного регулирования основности шлака
изменять содержание железной руды в рудной части шихты непосредственно
на доменной печи. Поэтому в рудную часть доменной шихты может входить до
5—10% железной руды (рис. 4).
Основными требованиями, предъявляемыми к железным рудам, агломерату и
окатышам, являются:
а) максимально возможное и постоянное содержание железа (допустимые
отклонения ±0,5%);
б) минимальное содержание серы и других вредных примесей (фосфор,
мышьяк, цинк);
в) ровный химический состав пустой породы (допустимые отклонения по
кремнезему, по окиси кальция и окиси магния +0,25%);
г) высокая механическая прочность и восстановимость;
д) ровный гранулометрический состав, отсутствие мелочи меньше 5 мм и
крупных кусков больше 60 мм.
В доменной плавке в сыром виде в основном используют магнетитовые и
гематитовые руды. Магнетит
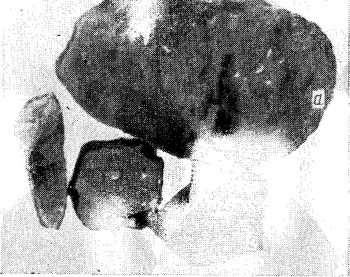
Рис. 4. Железные руды:
а — магнитогорская; б — таштагольская и криворожская
(Fe0-Fe203) черный минерал, имеет металлический
блеск, оставляет черту черного цвета, содержит 72,4% Fe. Его плотность
составляет 5,17 г/см3
Гематит (Fe203)—минерал, имеющий цвет от темного стально-серого до
темно-красного цвета, содержит 70,0% Fe. Его плотность 4,2—5,3 г/см3.
Часто встречается в соединениях с водой (Fe203 га Н20), в
зависимости от количества которой содержание железа изменяется от 59,8
до 69,0%. Плотность его соответственно колеблется от 3,6 до 5,4 г/см3, а
цвет руды изменяется от ярко-красного до красно-бурого, от темно-серого
до темно-красного, от темно-бурого до красновато-золотистого и желтого.
Окислы магнетита и гематита в земной коре залегают вместе с включениями
Si02, CaO, А1203, MgO, S, Р и др. Экономичность доменной плавки
достигается при максимально возможном удалении этих примесей различными
методами обогащения. Размеры отдельных кусков руды, добытой на руднике,
достигают до одного метра. Поэтому подготовка руд к плавке включает их
дробление, сортировку и усреднение. Конечной стадией подготовки железных
руд является производство агломерата или окатышей.
Сущность процесса агломерации заключается в том, что раздробленная до
0—3 мм, тщательно смешанная и увлажненная до определенной степени шихта,
состоящая из смеси руд и возврата с определенной добавкой коксика,
флюсов (известь, известняк, доломит), колошниковой пыли и окалины,
загружается слоем высотой 200—300 мм на колосниковую решетку движущегося
спекательного устройства. Под колосниковой решеткой создается разрежение
и через шихту просасывается воздух. С поверхности шихта нагревается до
1200—1300°С зажигательным горном, топливо шихты воспламеняется и
продолжает гореть за счет кислорода просасываемого воздуха. Горение
постепенно продвигается сверху вниз, образуя пирог агломерата.
При производстве окатышей связкой является глина — бентонит. В последнее
время есть тенденция вывода бентонита из шихты с заменой его обожженной
известью. Шихта окатышей состоит из железорудного концентрата (до 90%
фракций <0,074 мм), связки и флюса.
При производстве офлюсованных окатышей в шихту вводят известняк, однако
последнее время для уменьшения содержания серы (меньше образуется CaS)
его частично заменяют доломитом, что способствует также увеличению
содержания MgO в шлаках.
Материалы шихты тщательно смешивают, увлажниют и окомковывают в
тарельчатых или барабанных окомкователях. Процесс окомкования основан на
способности влажных, тонкоизмельченных материалов при перемещении их по
наклонной поверхности под воздействием капиллярных и молекулярных сил
формоваться в шарообразные гранулы. После окомкования сырые окатыши
загружают на движущуюся колосниковую решетку слоем высотой 250—300 мм. В
зонах сушки, подогрева, обжига, рекуперации и охлаждения газообразный
теплоноситель, пронизывая слой окатышей, создает условия для протекания
физико-химических и термических процессов. В результате этого в конце
обжиговой машины получаются окатыши, пригодные для доменной плавки.
Кроме ленточных обжиговых машин, для производства окатышей используют
шахтные печи, вращающиеся печи, работающие в комбинации с ленточными
машинами. При обжиге окатышей в шахтных печах их механическая прочность
выше по сравнению с окатышами, полученными на ленточных машинах. Однако
производительность шахтных печей намного ниже ленточных.
На качество окатышей, кроме вида обжига, большое влияние оказывает
минералогический состав руды. Установлено, что магнетитовые руды
формуются в окатыши лучше, чем гематитовые. .
За границей в основном налажено производство неофлюсованных окатышей. В
СССР производятся офлюсованные окатыши. При их производстве изменяется
характер пористости. Это связано с перерождением железорудных минералов
и изменением химико-минералогических и физических свойств. Окатыши
приобретают равномерную мелкозернистую структуру без заметных следов
сплавления. Однако процессы удаления серы при обжиге офлюсованных
окатышей замедлены. Наименьшее содержание серы наблюдается в окатышах
размером 12—13 мм. Поэтому такой размер окатышей является оптимальным
(рис. 5).
По химическому составу окатыши от агломерата отличаются содержанием
закиси железа. Так, если в агломерате содержание закиси железа
изменяется от 12 до 20%, то окатыши содержат 1—5% FeO. Наибольшая
механическая прочность окатышей составляет 700— 750 кГ/окатыш,
наименьшая прочность их равна 150—200 кГ/окатыш. Пористость окатышей
изменяется от 21 до 36%, объемная масса офлюсованных окатышей равна 2,1
г/см3. Окатыши с высокой механической прочностью имеют темно-серый цвет.
Качество рудного сырья определяется содержанием в нем железа,
прочностью, восстановимостью, зерновым составом. Так, нормально
спеченный агломерат имеет ровный гранулометрический состав и напоминает
губку с широко распространенной мелкой пористостью, содержит минимум
мелочи (0—5 мм) и кусков более 60 мм, не имеет видимых включений сырой
руды и флюса. В зависимости от состава спекаемых руд цвет агломерата
может быть от светло-серого или серебристого до вороненого. Форма кусков
агломерата округлая; наличие множества кусков неопределенной формы
указывает на недостаточную прочность агломерата (рис. 6).
Хорошо восстановимый агломерат имеет пористую структуру. Величина пор
3—5 мм. Наличие пор размером 10—15 мм свидетельствует о хрупкости
агломерата. Если агломерат сильно оплавлен, его структура
ноздревато-ячеистая с крупными оплавленными полостями (рис. 7).
Восстановимость такого агломерата пониженная.
Большое количество пыли, выделяющееся при выгрузке агломерата и
окатышей, указывает на их низкую прочность. Агломерат и окатыши с
повышенным содержанием мелочи (при одном и том же содержании железа )
имеют большую насыпную массу. Как неспекшийся, так и оплавленный (рис.
8) агломерат крошится в руках, при хранении образует много мелочи, из
бункеров доменной печи такой агломерат необходимо выбирать равномерно.
Горячий агломерат не должен выделять сернистого газа. Резкий запах
сернистого газа свидетельствует о недостаточной готовности агломерата.
Для оценки механической прочности агломерата пробу в количестве 20 кг
крупностью выше 40 мм загружают в барабан, диаметр и длина которого
соответственно равны 1,0 и 0,6 м. Барабан вращается в течение 4 мин со
скоростью 25 об/мин. После этого производят отсев фракции меньше 5 мм.
Количество этой мелочи, отнесенное к массе всей пробы и выраженное в
процентах, является показателем прочности агломерата.
Прочность окатышей характеризуют величиной механической нагрузки,
соответствующей моменту раздавливания единичного окатыша. Для этой цели
десять окатышей в окислительной, нейтральной или восстановительной
атмосфере при одной и той же температуре поочередно раздавливают,
нагрузка раздавливания записывается на ленте. Разработан также метод
определения разрушения под нагрузкой при температуре 1050° С в процессе
восстановления. С этой целью в ходе опыта измеряется убыль массы.
Восстановимость руд, агломерата, окатышей характеризуется скоростью
отнятия кислорода от окислов газом-восстановителем. В качестве
восстановительного газа используют водород или окись углерода.
Определение восстановимости производят при температурах 800— 900° С.
Методика определения на заводах различна. Такое многообразие методик
затрудняет сравнение рудного сырья разных заводов.
Для оперативного контроля изменения гранулометрического состава рудной
сыпи на участке загрузки доменных печей регулярно должен производиться
рассев агломерата, окатышей и руды по фракциям.
На отдельных южных заводах в рудную часть шихты постоянно вводят добавки
марганцевой руды. На остальных заводах СССР марганцевые руды используют
эпизодически в период расстройств хода доменных печей с целью получения
более подвижных шлаков.
Основным минералом, входящим в состав марганцевой руды и являющимся
устойчивым при обычной температуре и нормальном давлении, является
пиролюзит Мп02 (60—63% Мп). Этот минерал имеет черный или серо-стальной
цвет, полуметаллический блеск, оставляет черту черного цвета, плотность
его 4,8 г/сл3. В марганцевых рудах, используемых для выплавки
передельных чугунов, содержание марганца составляет 30—40%. содержание
кремнезема изменяется от 15 до 35%, а отношение содержания марганца к
содержанию железа равно 3—5. В основном применяют марганцевые руды
Чиатурского и Никопольского месторождений.
В доменной плавке используют также металлодобав-ки. К ним относятся
скрап и стружка. Скрап в бункера участка загрузки поступает после его
разделки в копровом цехе. Основными требованиями к металлодобавкам
являются чистота их от вредных примесей и отсутствие негабаритных
предметов. Стружка должна быть прессованной и незамасленной.
В случае нарушения технологии производства и получения агломерата и
окатышей пониженной или повышенной основности для поддержания
оптимального шлакового режима доменной плавки используют флюсы (кислые
или основные). Ценность основного флюса — известняка определяется
содержанием в нем окиси кальция СаО. В качестве кислого флюса в основном
применяют кварцит, основным компонентом которого является кремнезем
SiO2.
|
|
|